Across the northern and central provinces of Laos, Lao Tobacco Limited (LTL) plays a key role in producing quality tobacco for the country. At the heart of this operation is the company’s main factory, an environment where skilled workers and innovative processes come together to deliver top-tier products.
Leading this hub of activity is Xayadeth Bounbansy, the factory manager with nearly two decades of experience at LTL.
Sitting in a cozy guest room at the factory, dressed in his company uniform, Xayadeth shared what makes the LTL factory more than just a workplace.
Growing Skills, Facing Fears
One of LTL’s top priorities is developing the abilities of its employees.
Workers are trained to operate multiple machines, allowing them to stay flexible and take over different tasks when needed.
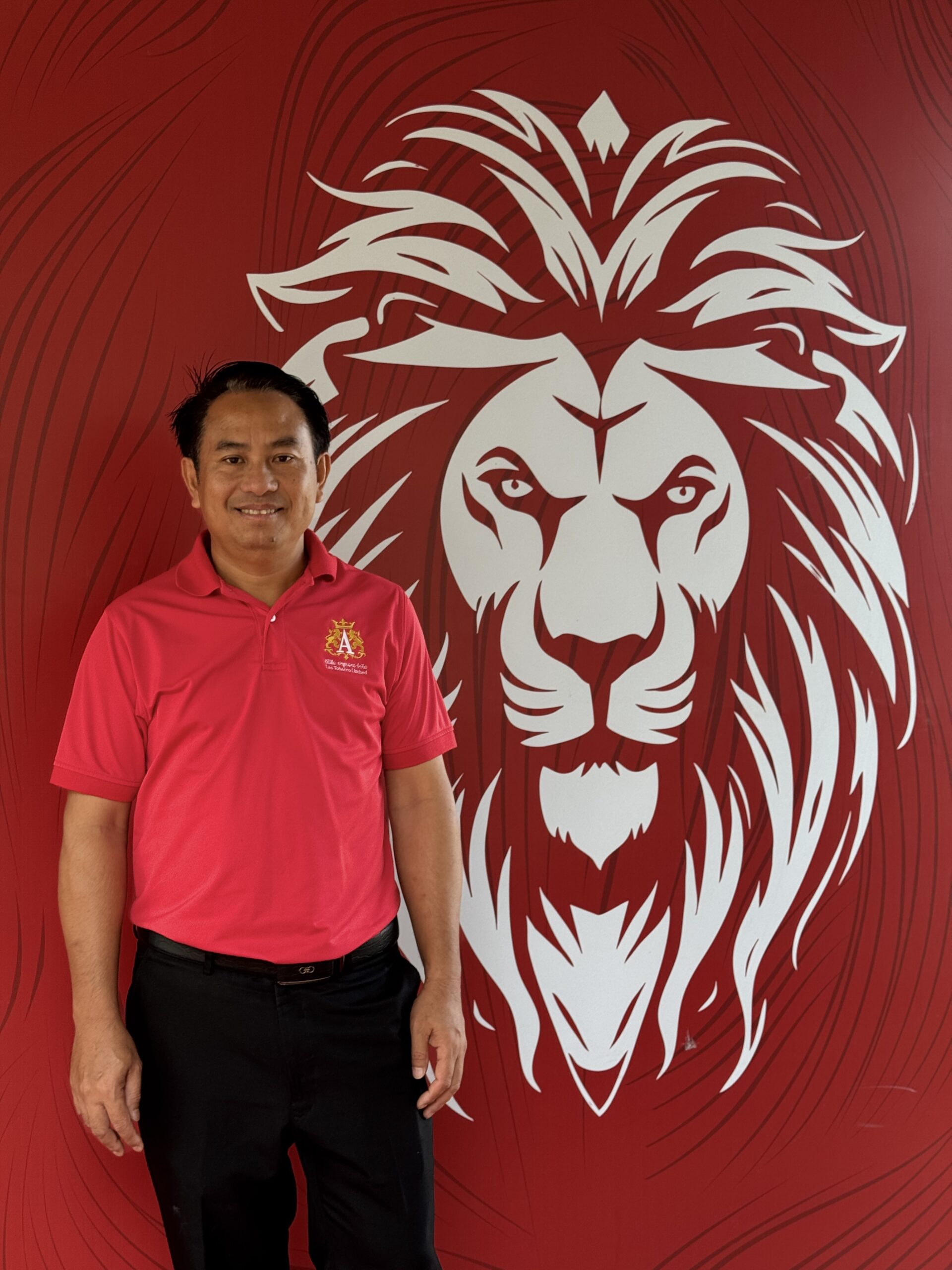
“We want our workers to be well-rounded,” Xayadeth said.
“Each machine requires different technical skills, and learning to run them helps our team become more versatile.”
This multi-skill training allows the factory to remain productive even when someone is absent, and it prepares workers to handle different roles throughout the production line. It also fosters stronger problem-solving capabilities, as workers learn to troubleshoot issues on the spot.
Training is conducted both locally and internationally.
Department managers also actively participate in sessions alongside their teams to better understand the skills being taught and the challenges workers face.
“Managers don’t just supervise,” said Xayadeth. “They join the training, share the experience, and grow with the team.”
Select workers also have the chance to travel to LTL’s international branches in Germany, Poland, the Dominican Republic, Spain, and Hungary.
During these one- to two-week trips, they receive exposure to new production technologies, machine upgrades, and new manufacturing techniques.
Despite all this support, stepping into new technical roles can be intimidating.
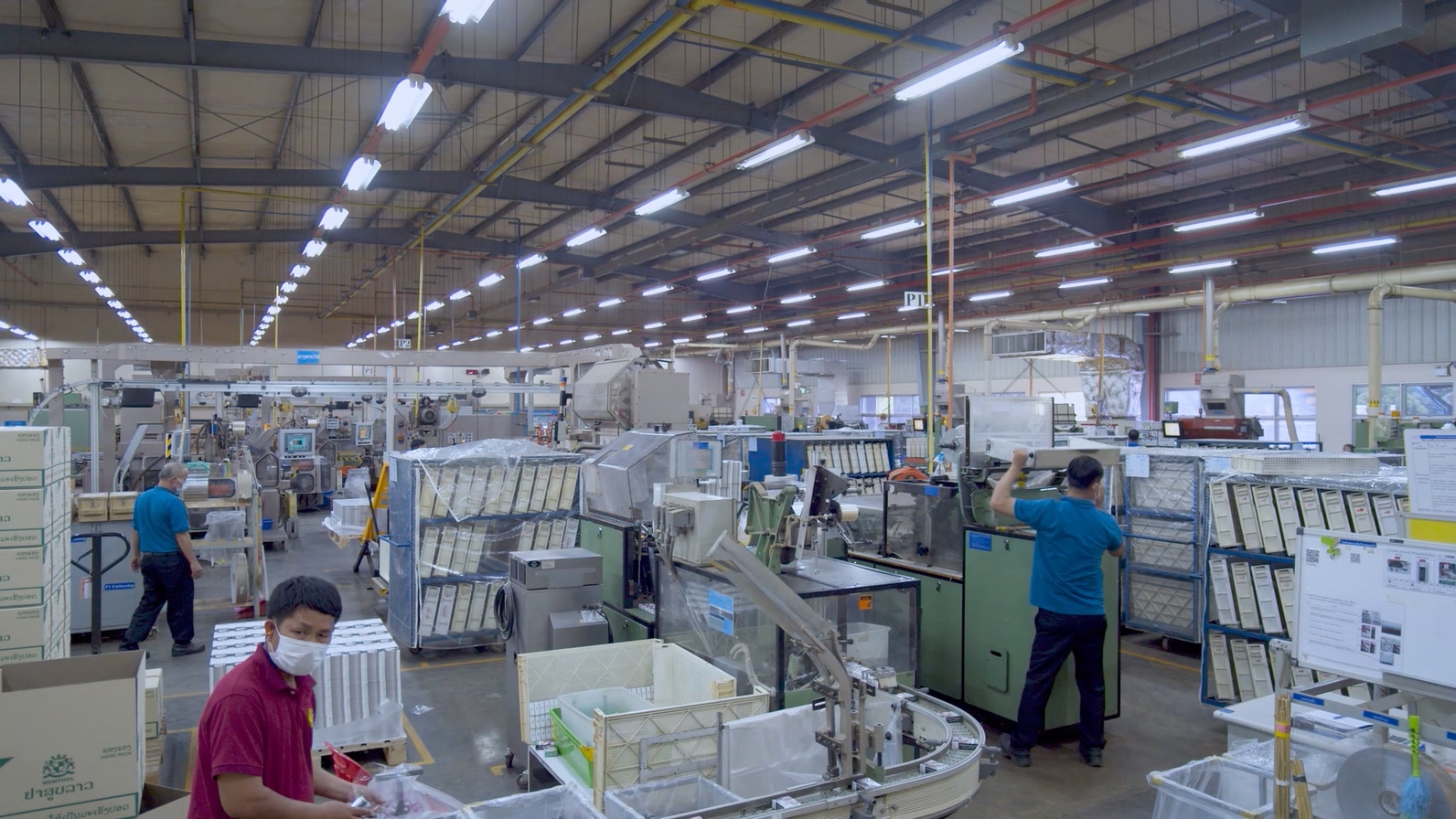
“Some workers try to take on harder tasks but get stuck in what I call the ‘fear zone,’” Xayadeth explained. “If they can overcome that, they enter the learning zone, where real growth happens.”
He emphasized that while factory-specific machine knowledge may not transfer directly to other industries, the critical thinking, attention to detail, and adaptability gained at LTL are valuable anywhere.
“People who’ve worked here often find it easier to get jobs elsewhere,” he said. “That’s because they develop strong, well-rounded skills that employers value.”
A Workplace That Cares
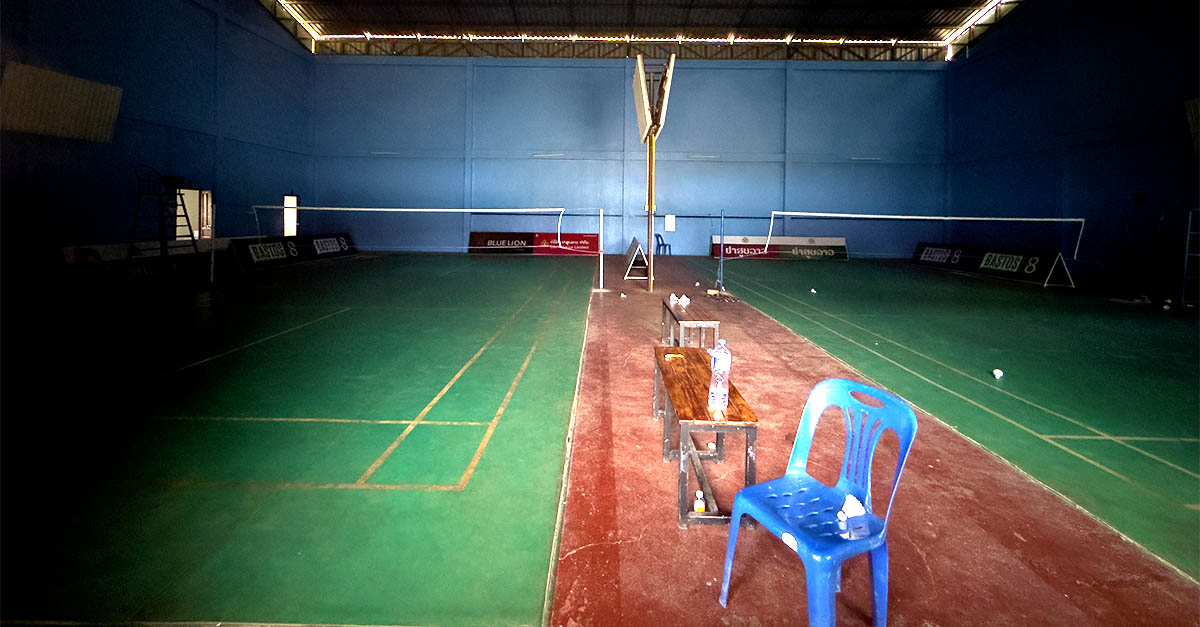
Beyond professional development, LTL is committed to the well-being of its employees. The factory offers a range of recreational facilities, including a room with a TV, table football, books, badminton courts, and a French petanque field.
“We want our employees to have time to relax,” said Xayadeth. “They can enjoy these facilities during lunch breaks or after work.”
The company also ensures that meals served in the cafeteria are clean and safe, contributing to employees’ overall health.
Putting Safety First
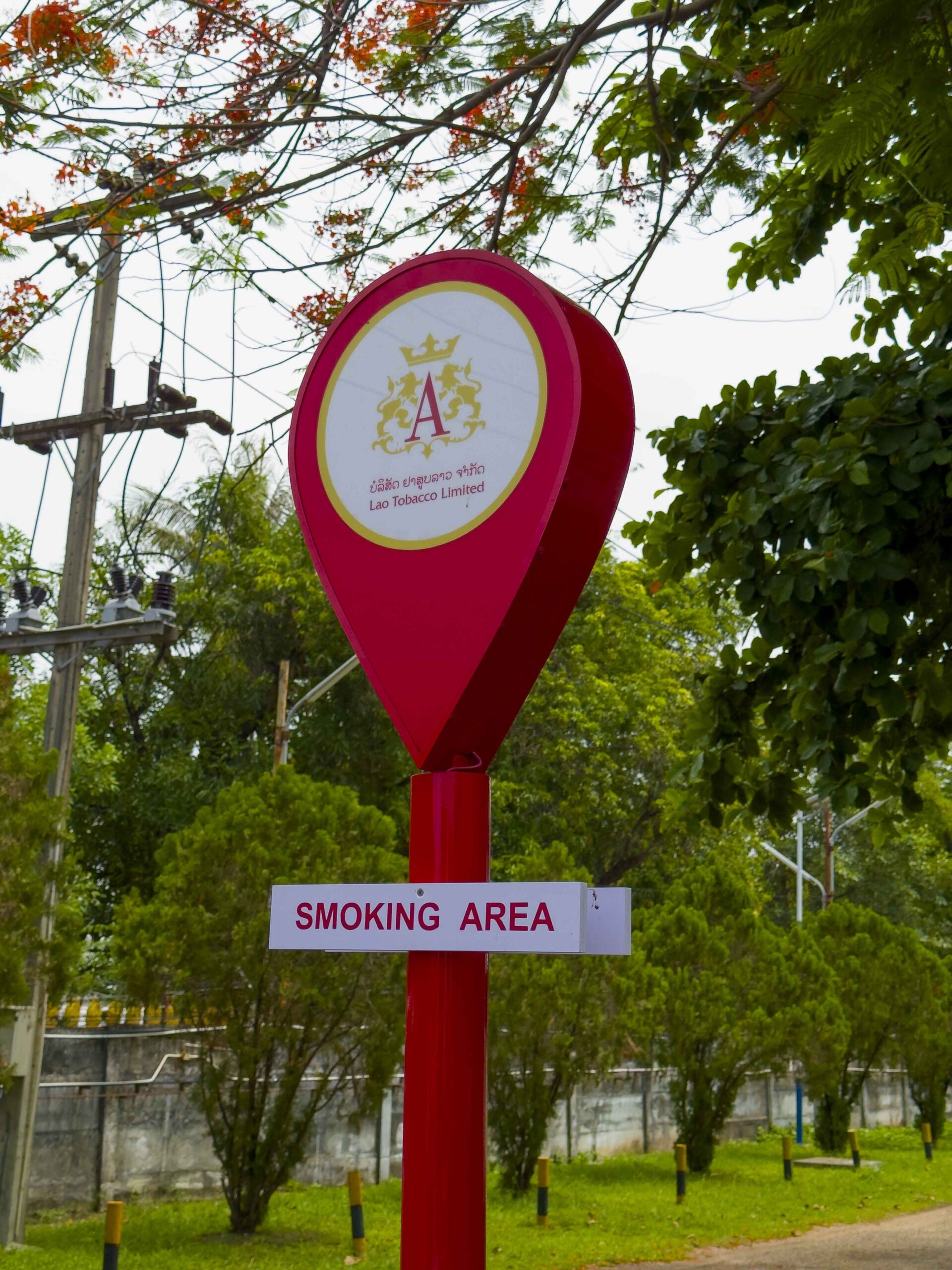
LTL also places a high priority on workplace safety. Designated smoking areas are strictly enforced, and all individuals entering the factory, including outside contractors, must undergo safety training.
“Whoever works with us or even visitors need to undergo safety training to ensure their own safety and the safety of our workers,” Xayadeth said.
The factory also conducts daily safety discussions to identify and manage risks in the working environment.
This proactive approach has paid off: the factory has gone over six years without a “lost time accident,” a testament to LTL’s dedication to keeping its people safe.
A Place to Grow
The factory team is made up mostly of workers around the age of 39, with 18 percent being women. However, age is never a barrier.
“We don’t look for a specific age group. What matters is their willingness to learn and grow with us,” said Xayadeth.
That commitment to growth is reflected in how long employees stay with the company.
Some have been with LTL for as little as seven years, while others have worked there for up to three decades, according to the manager.
For Xayadeth and his team, the factory is more than a production site, it’s a place where people develop not just professional skills, but confidence in themselves.